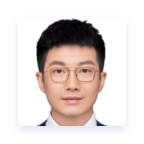
Research Interest
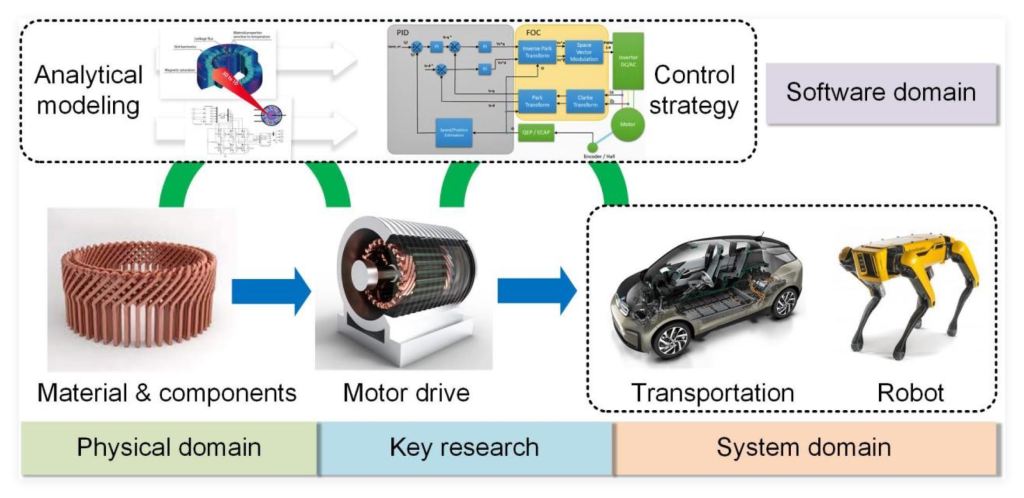
Motor drives consume about 50% of electricity in modern society, and it directly influences the performance of robots and electrified transportation. Our research goal is to push forward the boundaries of the motor drive in both the physical domain and software domain. By adopting the advanced material, manufacturing method, analytical modeling, and control strategy, we hope to design motor drive systems with high power density and high control accuracy to promote intelligent industrialization further. Specifically, Dr. ZHAO's research focuses on energy conversion and autonomous systems with emphases on
1) design, modeling, and optimization of motor topologies;
2) power electronics and control strategy for motor drives;
3) application of motor drives in robots and electrified transportation.
(1) High-fidelity multiphysics analytical modeling of motors
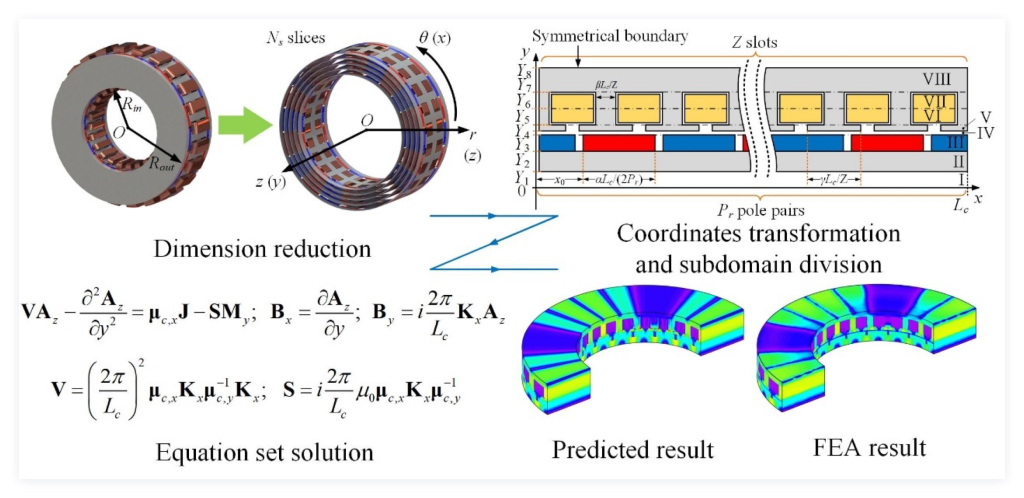
When applied to novel motor topologies (such as magnetic field modulated motors and axial flux motors), commercial finite element analysis (FEA) methods will encounter problems such as complicated meshing and long computation time. Aiming at this phenomenon, Dr. ZHAO used the analytical modeling method to construct the mathematical model for motors, which can significantly improve the calculation efficiency of the motor's electromagnetic field parameters and shorten the motor's design cycle. Taking the case of axial flux motors, Dr. ZHAO applied the Fourier series method in the complex form to the electromagnetic parameter calculation of this type of motor. The proposed method can save nearly 40% time compared with FEA without reducing the calculation accuracy. The research group will further study the high-performance analytical modeling method of multi-physics fields, such as the motor's mechanical structure and temperature field, and then apply it to the comprehensive design and analysis of the motor drive system.
(2) Next-generation integrated motor drive system for robots
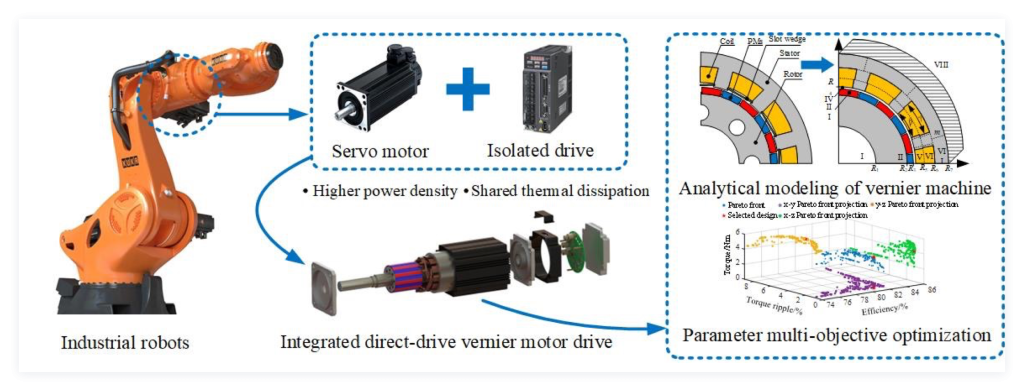
The research, development, manufacturing, and application of robots are essential indicators to evaluate the level of a country's technological innovation and high-end manufacturing. At present, the joints of robots are mainly driven by a permanent magnet synchronous motor with a reduction gear. However, this technical solution has many disadvantages: the precision reduction gear is expensive; the mechanical vibration and noise are significant; the maintenance cost is high. Besides, the developed countries have already monopolized this technology. Dr. ZHAO designed a direct drive/semi-direct servo system by adopting a vernier machine as the actuator component to replace the existing technical solution. Then, Dr. ZHAO used the aforementioned complex Fourier series method to conduct geometrical-parameter multi-objective optimization of the vernier machine, and the optimization efficiency was greatly improved. The next-stage plan of the research group is to design a servo system that integrates corresponding high-efficiency actuators and drive circuits in combination to satisfy the actual needs of various robot application scenarios such as footed and wearable robots.
(3) High-power-density motor drive for electrified transportation
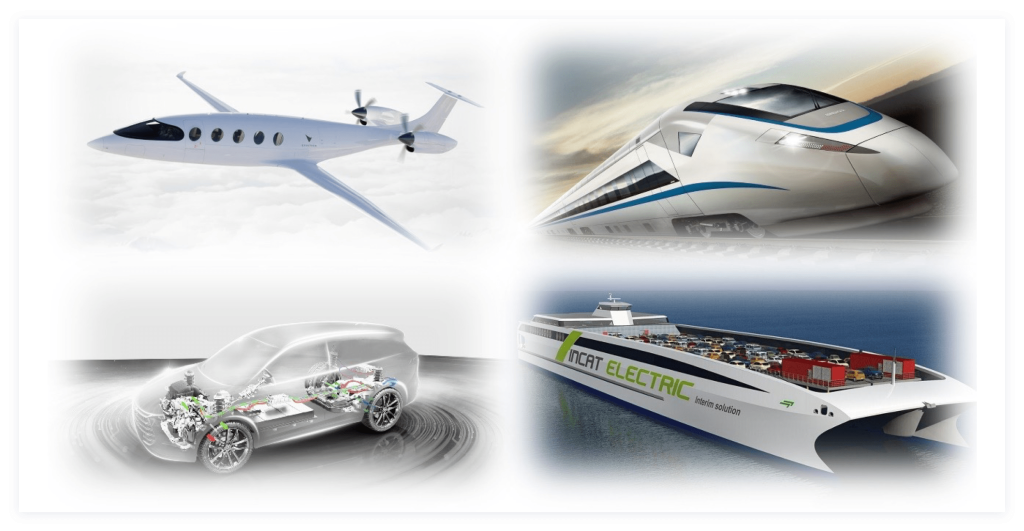
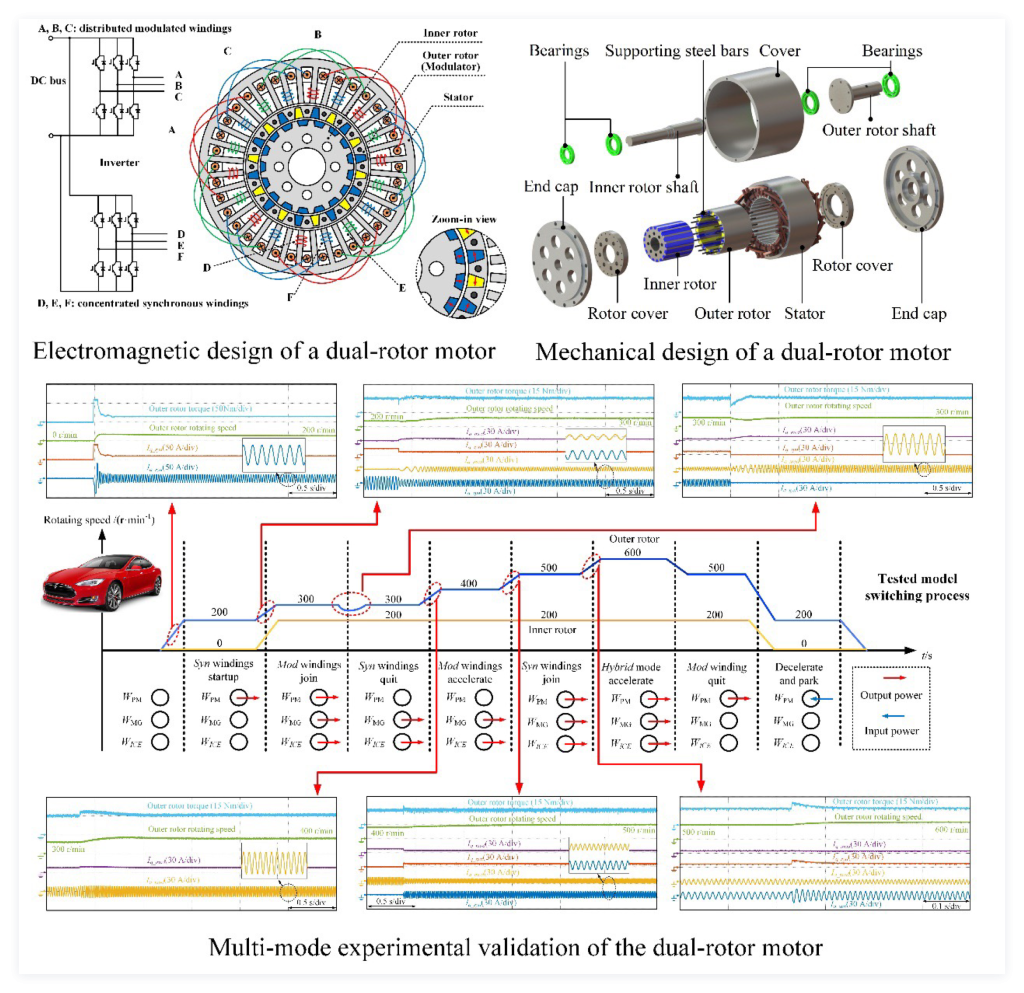
Electrified vehicles are gradually becoming popular with the continuous development of motor topology and power electronics technology. Limited by the energy density of batteries, the mileage of pure electric vehicles at this stage is still difficult to meet the needs of long-distance travel and freightage. Therefore, hybrid vehicles will be the optimal solution for a long time in the future. Taking a hybrid vehicle as an example, Dr. ZHAO proposed a high-performance consequent-pole dual-rotor motor to replace the existing mechanical power distribution device and motor structure. The new structure reduces the vibration and noise of the system and improves the overall compactness. Dr. ZHAO completed the motor's design, optimization, and control and verified the feasibility of mode-switching between various operating conditions of the prototype based on the new standard European cycle test (NEDC). In the future, the research group will design corresponding high-power density motor drive systems according to various vehicles' structural and operating characteristics to improve their comprehensive performance.
Achievement Transformation
The research outcomes can be used to address the following problems:
1. Commercial finite element software is too long to simulate the three-dimensional electromagnetic field of the motor. The proposed method can shorten the calculation time of the electromagnetic field and improve the calculation efficiency. This method has the potential to be applied in the preliminary design of various types of motors, such as motors for household appliances and wind turbines for wind farms.
2. The existing industrial robot actuators have a low integration level. The proposed integrated high-torque high-power-density direct-drive motor can eliminate the use of reduction gear or reduce the reduction ratio. This topology can be applied to actuators in industrial robots and service robots.
3. Currently, the torque/power density of the propulsion motor of electrified transportation is not high enough. The proposed new axial flux motor can further increase its operating speed and torque. This motor structure can be applied to new energy vehicles, electrified aircraft, ships, etc.