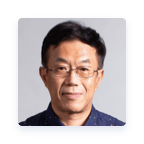
Multi-pass flank milling on complex parts based on stripification

Technology
Multi-axis flank milling is widely used due to its higher cutting efficiency and better surface finish quality than point milling. The traditional flank milling only applies to a simple parametric surface and usually generates a single tool pass, which is incapable of handling a complex part. Here we develop a new multi-pass flank milling method that allows a complex surface to be machined by multiple flank milling tool paths. This method constructs a vector field to guide the directions of strips that approximate the part surface, i.e., stripification, and for each strip, a flank milling tool path is generated subject to various machining constraints.
Potential Applications
- Multi-axis flank milling
- Robotic hot wire cutting
- Electrical discharge machining
Advantages
- High efficiency
- Smooth and interference-free tool paths with high accuracy
- Aesthetic surface morphology
Hybrid manufacturing
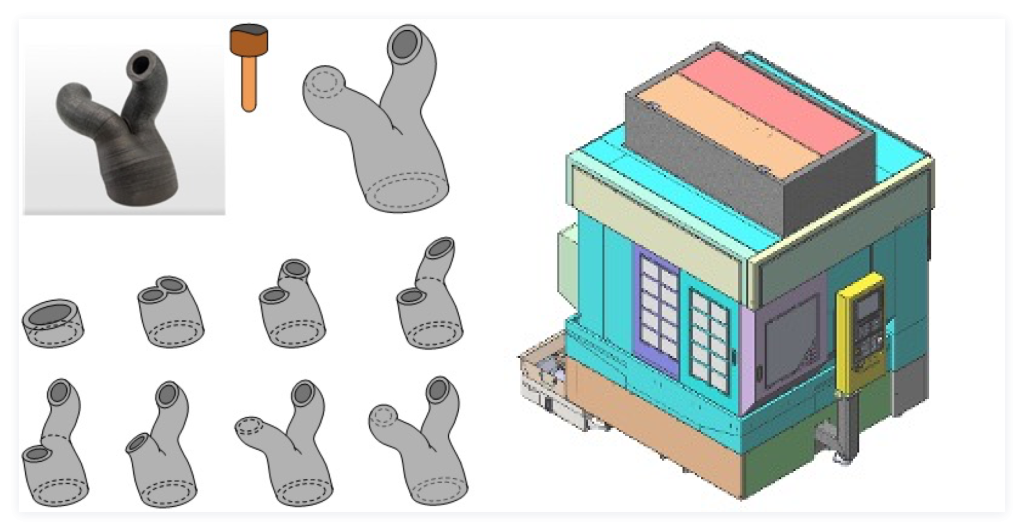
A hybrid platform integrating the subtractive and additive process and can perform them alternatively is able to manufacture complex manifold previously unattainable either by subtractive or additive processes. We have developed a graphic based manufacturability analysis algorithmic framework to solve for the best alternating sequence that yield collision free process with least alternation. And we are developing a hybrid manufacturing center that integrating additive and subtractive process as well as non-destructive testing module based on laser ultra-sound.
Multi-axis CNC trochoidal milling process planning

The conventional trochoidal milling is two-dimensional in nature, which can only be used to machine the cavity in 2D shape. We first proposed the method for optimizing the machining efficiency in 2D trochoidal milling method, in which the novel cubic curve-based trochoidal milling tool path is proposed. Thereafter, we proposed a five-axis trochoidal milling strategy applicable to machining more complex 3D shaped cavities, and thus further extended the application of trochoidal milling. For further improving the effectiveness and feasibility of the 3D trochoidal milling method, we proposed the kinematics optimization strategy for improving the kinematics performance of the CNC machine tool in the trochoidal milling process, and the multi-layer trochoidal milling strategy for tackling the deep curved 3D slot, e.g., the blade slot.
Process planning of multi-axis additive manufacturing
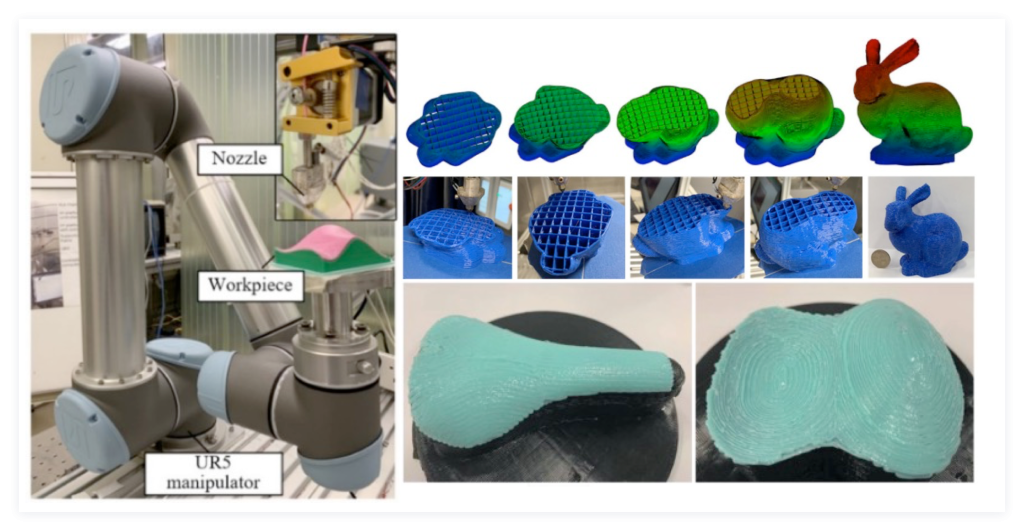
Additive manufacturing (AM) is currently a promising manufacturing technique to be applied in different industrial sectors. Based on the long-term research experience and deep understanding in five-axis machining, my group investigates multi-axis AM to explore the full potential of AM. By utilizing the rotational axes and adopting curved printing layers, the problems in conventional 2.5D AM, such as excessive supports and poor mechanical properties, can be overcome. After the endeavor in past few years, our group has built a homebuilt multi-axis robotic printing system and developed several algorithms in curved layer slicing and multi-axis printing path generation. Our results have been published in the international journal.