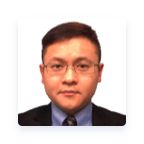
Advanced fabrication of carbon nanomaterials
We studied how the competition between temperature-driven dissolution and precipitation of carbon atoms governs the sp2 carbon lattice (i.e. graphene) nucleation and growth kinetics on various substrates including thin metal films, nanowires, and nanoribbons. A highly dynamic chemical vapor deposition (CVD) process was developed to rapidly grow monolayer graphene with extraordinary quality on nanostructured substrates while avoiding solid-state dewetting at high temperatures. Importantly, this rapid segregation-mediated synthesis method is widely applicable for other 2D crystals (e.g. h-BN, MoS2).
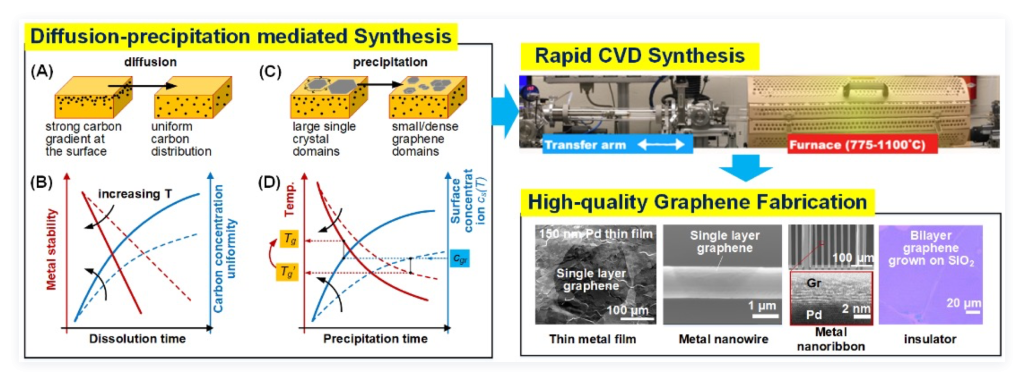
In addition, we developed an interfacial graphene synthesis route that can result in highly uniform graphene patterns directly on insulating substrates. The process involves forming the thin film metal catalyst on a dielectric substrate, followed by rapid thermal treatment of the catalyst in a hydrocarbon environment to induce the dissolution of carbon atoms into the metal and nucleation of graphene at the metal-substrate interface upon cooling. Removing the top metal layer mechanically or chemically directly leaves the graphene layer on the dielectric substrate. As-fabricated graphene patterns on target substrates can be used for applications such as thermal management of electronics, surface treatment for defouling and condensation enhancement, surface hardening, to name a few.
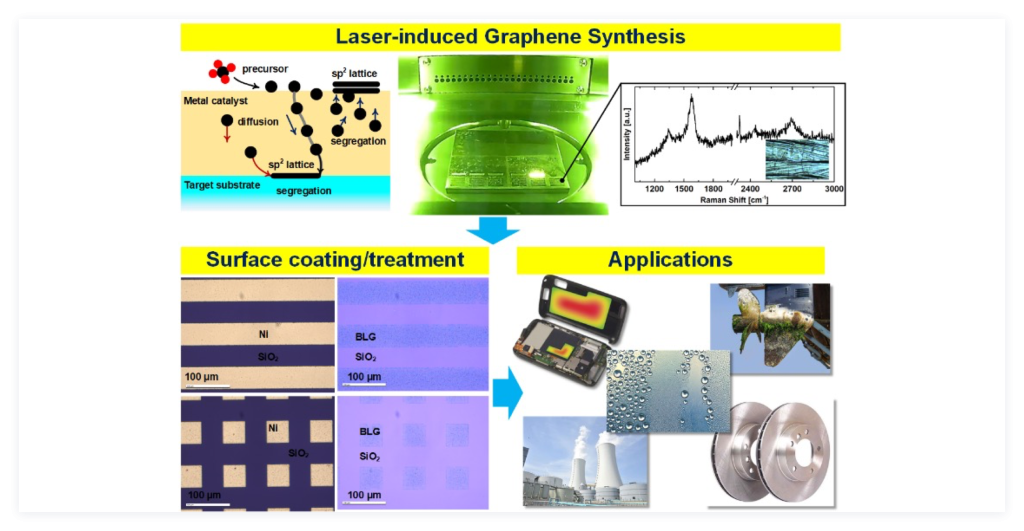
Metal matrix composites design and manufacturing
We demonstrated that CVD-grown graphene-metal thin film nanocomposites possess significantly higher mechanical properties exceeding the rule of mixture. We characterized as-grown graphene-metal thin films using various nanomechanical testing modalities and observed unusual fracture behaviors, showing notably high toughness, which is an order of magnitude higher than that for a bare thin metal film. Our recent experiments exhibited an over 100% increase in devices’ stretchability using as-grown graphene-metal interconnects. All these plasticity and elasticity reinforcements are decisive in thin films’ applications in flexible electronics for wearable devices. In addition, high quality, high mechanical integrity, and flexible architecture design of the proposed in-situ synthesis of graphene-metal interfaces shed light on the route towards the next-generation metal matrix composites for the fields such as the aerospace industry, transportation, and power electronics.
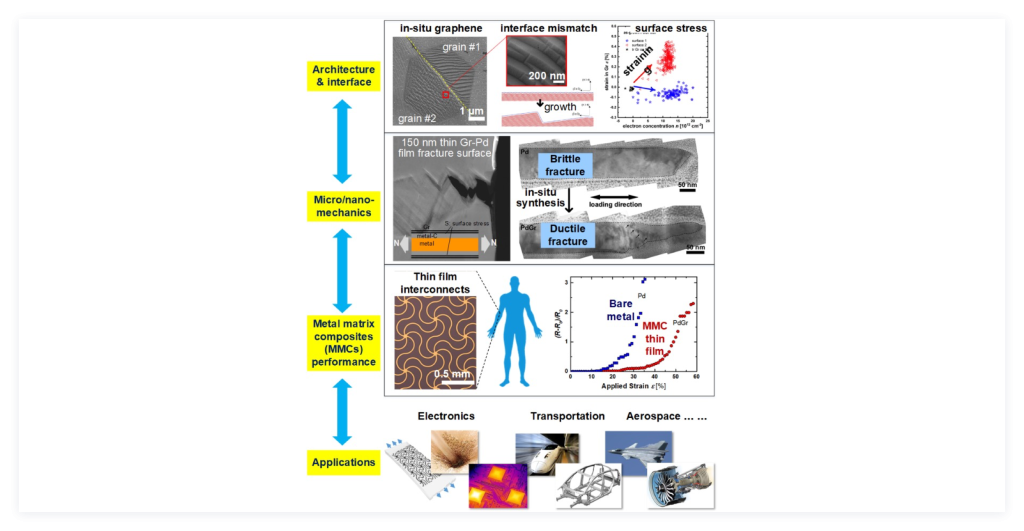
Dropwise digital printing of metals
Many established metal additive manufacturing (AM) processes involve layer-by-layer deposition and selective binding or melting of metal powders. However, these processes do not easily permit multi-material printing or printing directly onto non-planar surfaces. By contrast, AM techniques that deposit metal directly are typically low resolution (e.g., directed energy deposition), or cannot achieve bulk metal properties (e.g., ink-based methods). We proposed a novel hybrid metal AM method involving on-demand deposition of discrete metal microdroplets (10-100 µm), which are produced by electrohydrodynamic (EHD) ejection followed by in-flight laser melting. This new approach decoupled the metal microparticle melting and the feedstock feeding processes and therefore overcame the well-established limitation of direct metal jetting techniques that must maintain a high-temperature liquid metal reservoir. We can further utilize this design to achieve high-resolution refractory metal printing, advanced alloy and multi-metal AM, and functionally graded material manufacturing.
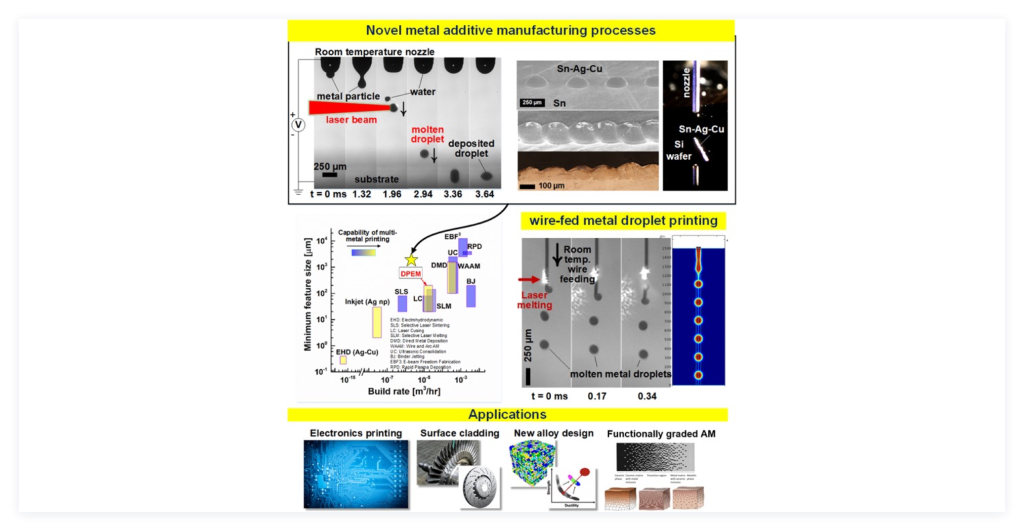