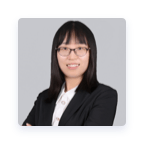
Modeling and online process monitoring of high-density 3D point cloud data based on sparse learning
Online process monitoring and control are important for product quality and process safety in manufacturing systems. With the rapid development of 3D scanning technology, high-density point cloud data can be generated by 3D scanners in complex manufacturing systems. However, due to the complexity and large volume of high-density 3D point cloud data, there is a lack of effective methods for modeling and monitoring the manufacturing process based on such type of data. The target of this research is to develop sparse-learning-based methodologies for modeling and online process monitoring of high-density 3D point cloud data. Specifically, with the considerations of defect sparsity and types, theories of sparse learning will be fully investigated for high-density 3D point cloud modeling and fast parameter learning to realize precise defect detection and classification. In addition, an online monitoring scheme will be proposed for fast analyzing high-density 3D point cloud data by fusion of engineering domain knowledge and sparse learning theory. Hopefully, this research could provide a solid theoretical basis and key technologies for real-time high-density 3D point cloud data processing and online process monitoring in manufacturing systems.
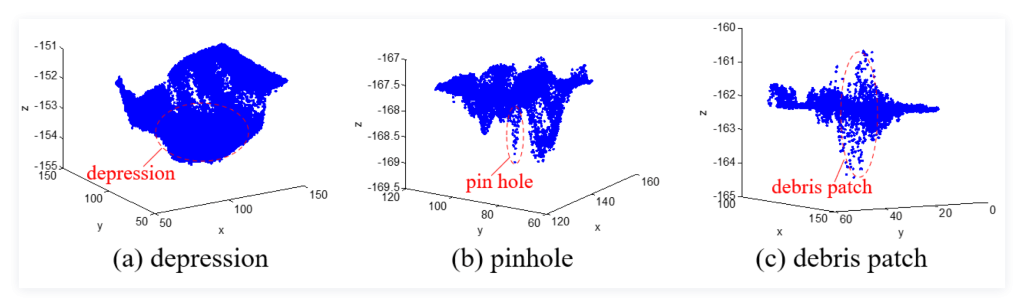
Fig. 1. Illustrations of three types of defects on steel surfaces: (a) depression, (b) pinhole, and (c) debris patch
Figure 1 illustrates three types of defects on steel surfaces: (a) depression, (b) pinhole, and (c) debris patch by using 3D point cloud data. It is very important to detect and identify these anomalies for quality inspection and improvement of manufacturing processes. This research hopes to systematically integrate sparse learning theories and data decomposition for precise anomaly detection and identification.